Characteristics of Three-Dimensional Triangular Wound Core Transformer
1. Low Loss and High Efficiency
· Continuously wound core design with no air gaps and low magnetic resistance, reducing no-load loss by 20%-30% compared to traditional laminated core transformers, improving energy efficiency and reducing operating costs.
· Low no-load current: The uniform and continuous magnetic circuit requires 20%-50% less excitation current, minimizing reactive power loss in the grid.
2. Balanced Three-Phase Magnetic Circuit with Superior Electromagnetic Performance
· Equal-length three-phase magnetic circuits eliminate the imbalance found in traditional E-type or laminated structures, ensuring balanced three-phase excitation currents, reducing harmonics, and improving power quality.
· Low noise: The continuous wound core process minimizes magnetic hysteresis vibration, reducing operating noise by 3-5dB compared to conventional transformers, making it suitable for noise-sensitive environments such as residential areas, hospitals, and schools.
3. Compact Structure, Smaller Size, and Material Savings
· The three-dimensional triangular structure allows windings to closely wrap around the core, shortening the average turn length and reducing copper losses, thus improving electromagnetic conversion efficiency.
· Occupies 20%-30% less space, making it ideal for compact installations such as urban substations, underground power distribution rooms, and box-type substations.
4. High Mechanical Strength and Strong Short-Circuit Resistance
· Since the windings are evenly distributed around the triangular core, the mechanical stress is balanced during short circuits, improving short-circuit resistance by 20%-30%, making it particularly suitable for grids with frequent voltage fluctuations.
· Uses high-strength clamping and an integrated frame structure to enhance overall stability and reduce damage risks from short-circuit impacts.
5. Low Temperature Rise and Excellent Heat Dissipation
· Windings are tightly attached to the core, reducing heat dissipation distance and improving cooling efficiency, leading to lower temperature rise and an extended transformer lifespan.
· Natural air cooling or forced air cooling design, making it suitable for high-temperature environments or continuous heavy-load operations.
6. Advanced Manufacturing Process for Greater Consistency
· Automated winding technology minimizes human errors, enhancing product consistency and reliability.
· Fewer welding points reduce contact resistance, improving operational safety.
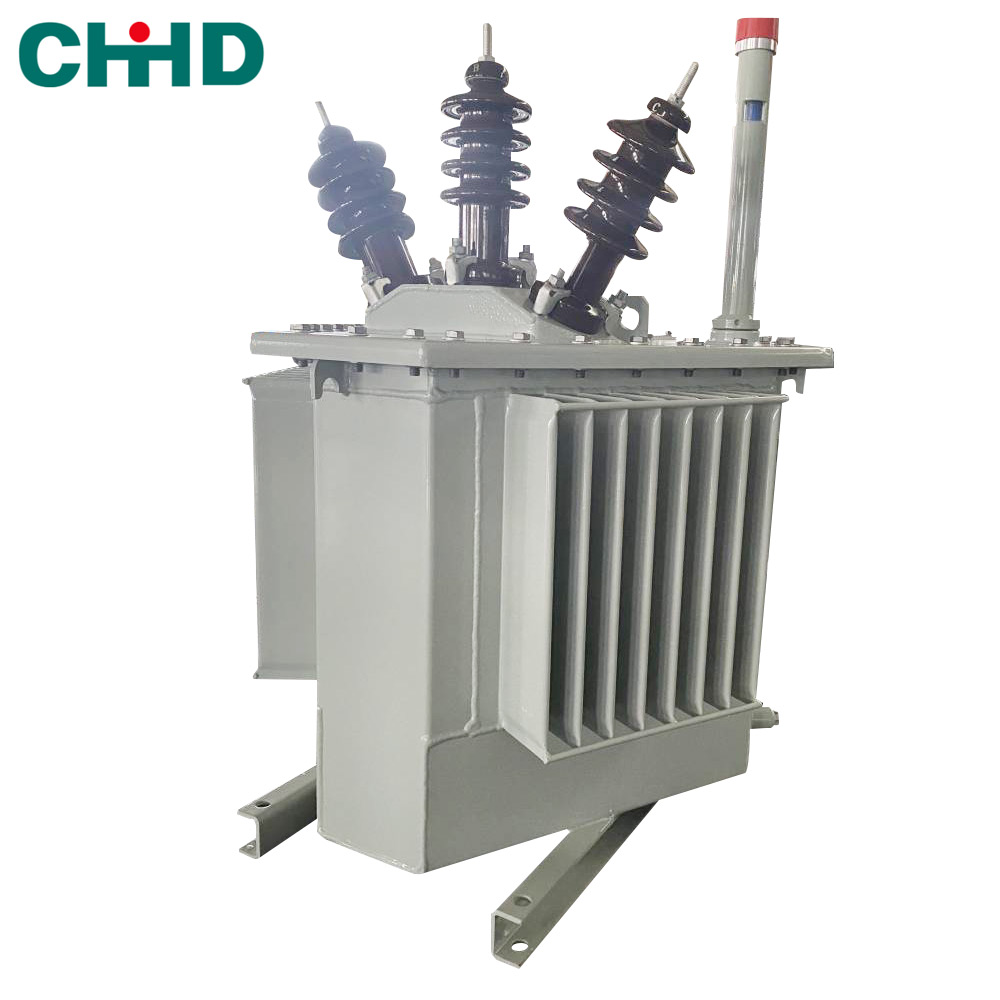
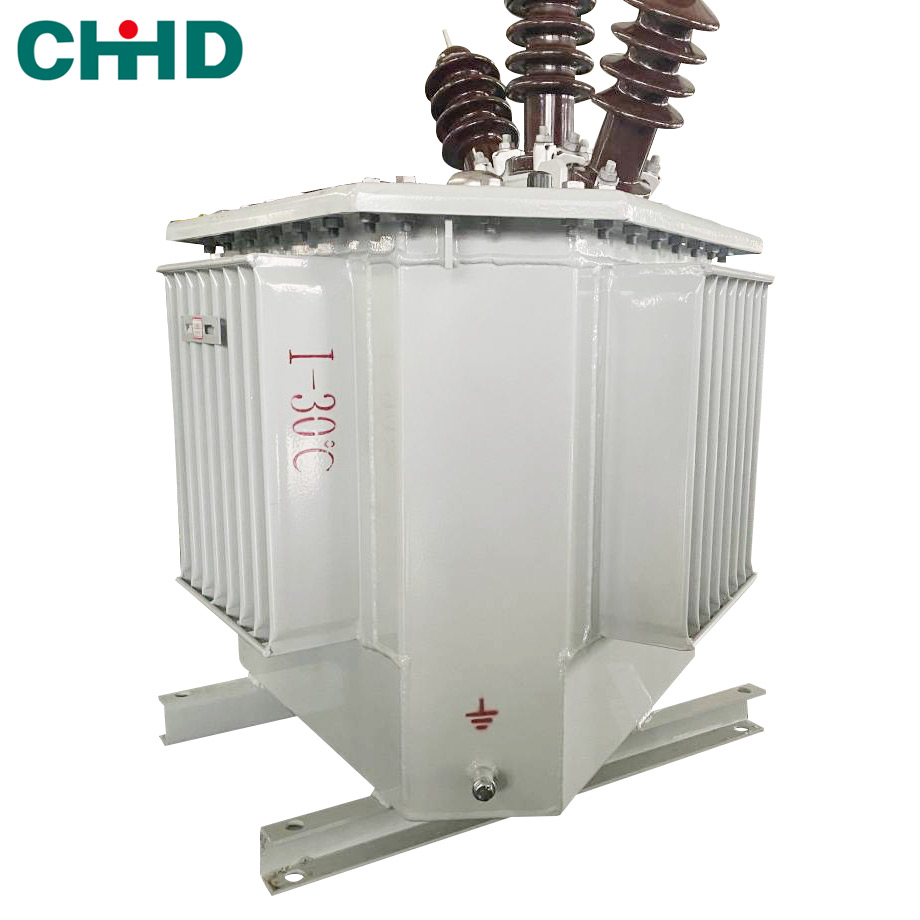
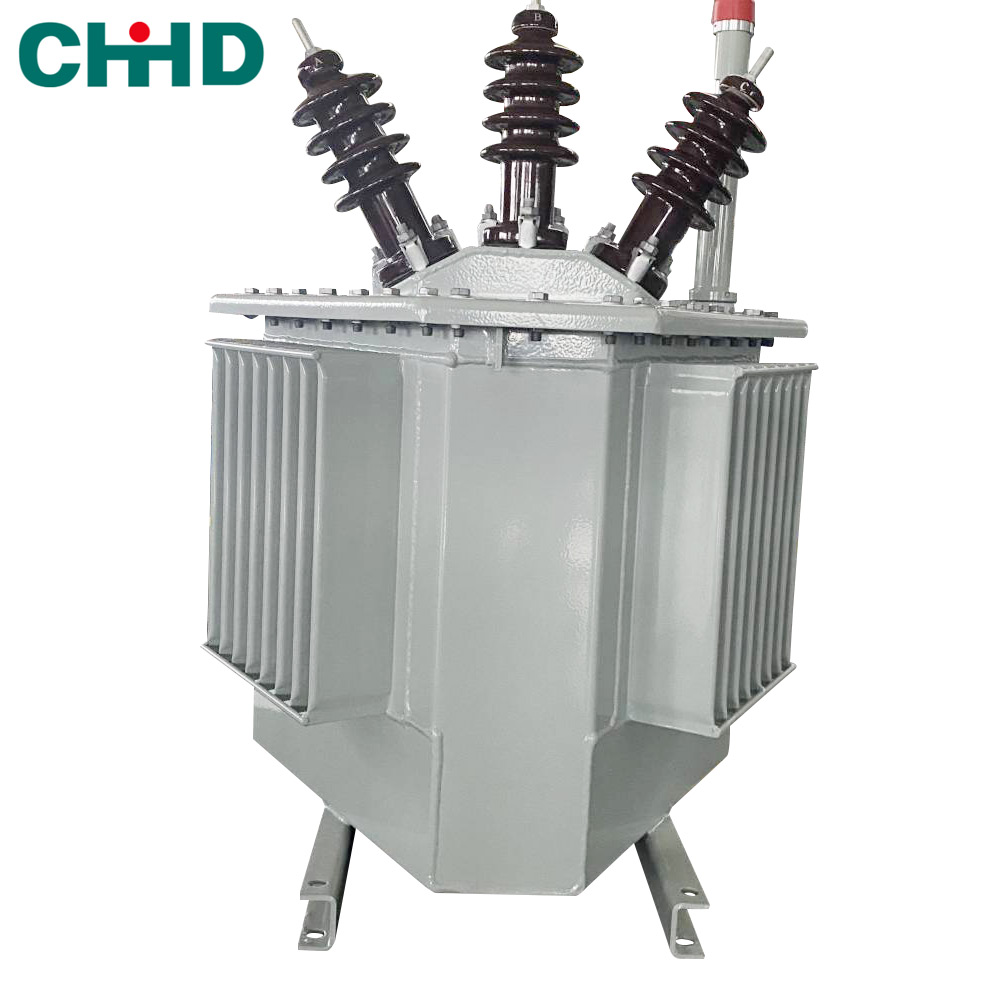
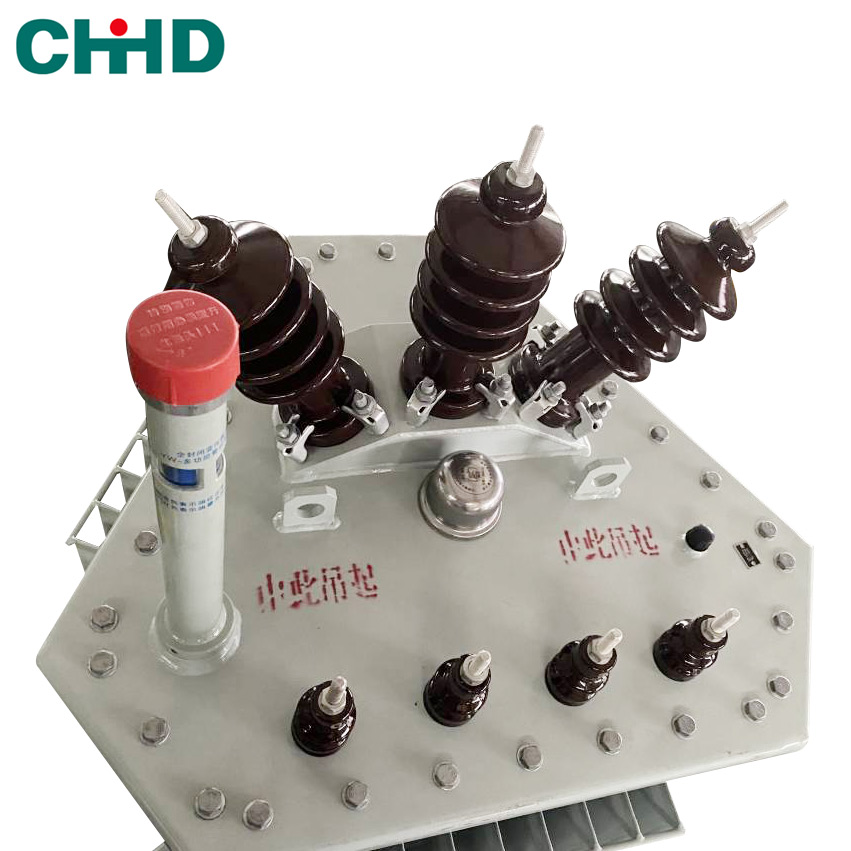
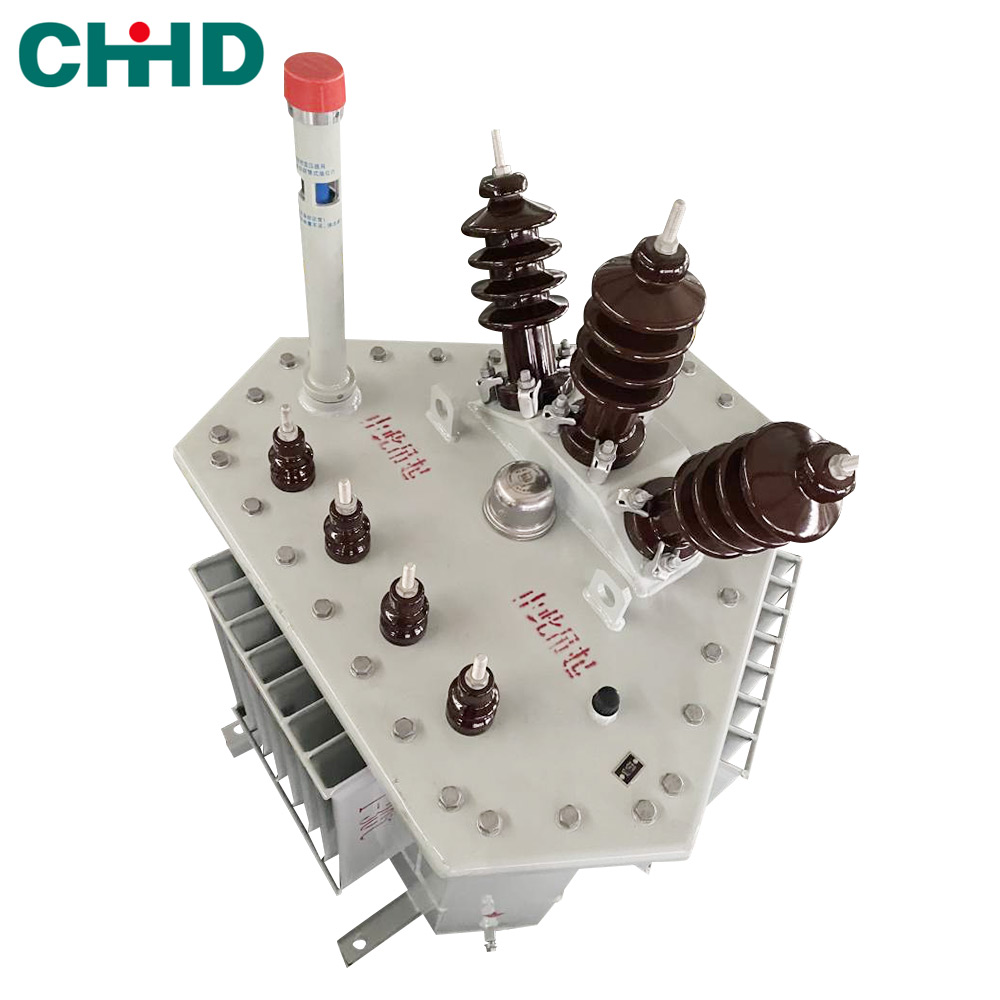
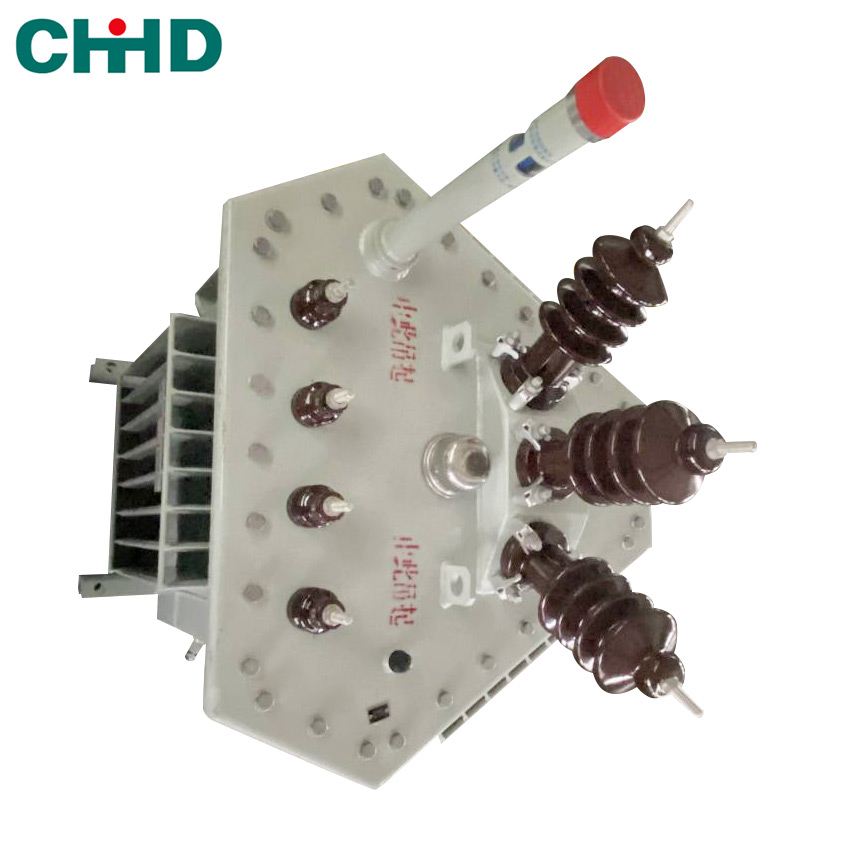
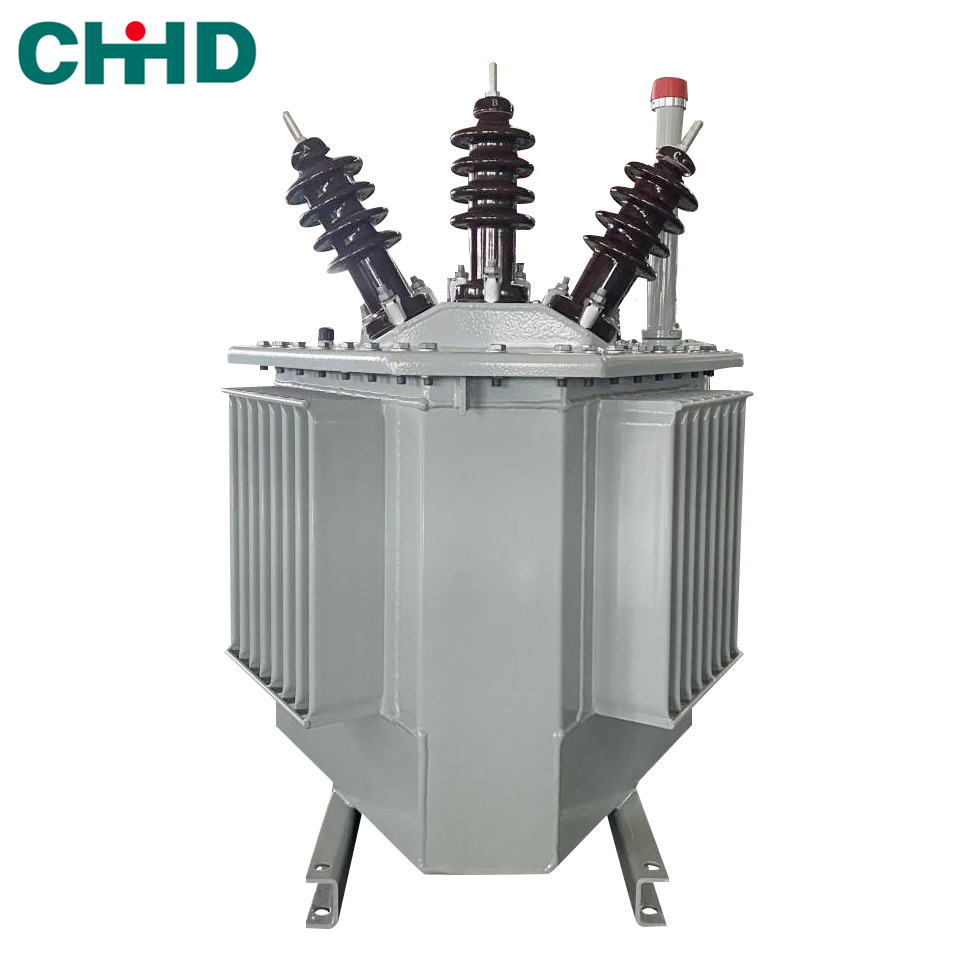